Increasing Power Density in Industrial Engines is Transforming the Market with a Focus on Structural Strength of Key Components. Higher efficiency and better performance are the fundamental pillars characterizing any new product launch in the engine segment. These concepts ensure that the latest generations of engines offer performance levels equal to or exceeding those of previous generations, with lower fuel consumption and reduced energy dissipation. These results are often accompanied by weight and size reductions.
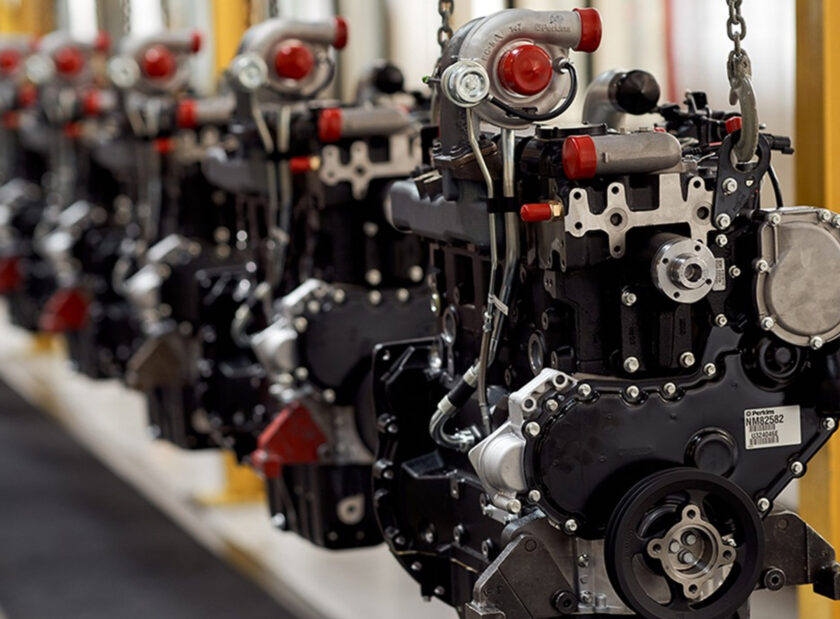
Objective: Power Density
The need to reduce emissions in compliance with increasingly stringent regulatory levels has led to the constant optimization of combustion processes. This is also thanks to the introduction of more efficient turbocharging and fueling systems, supported by more sophisticated electronic controls. These solutions aim to improve the lubrication and cooling of components.
In this context, the engine industry has been, and still is, able to meet the downsizing requirements in industrial applications by increasing power density and reducing unit dimensions. However, smaller engines mean more stressed components that must offer reliability levels equal to or greater than those of previous generation engines.
Structural Design
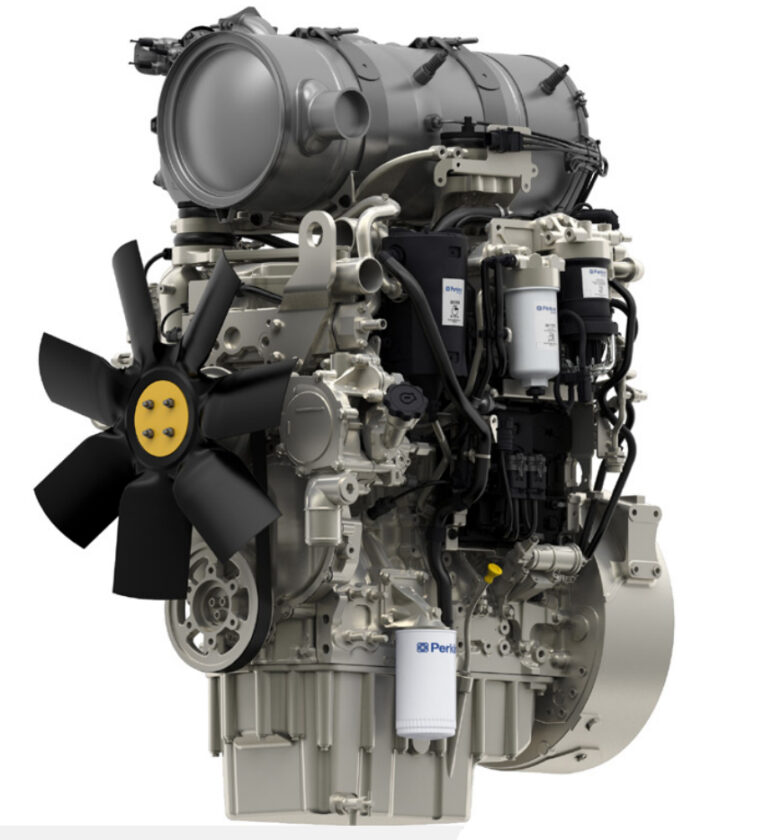
Therefore, the contribution of structural design divisions for units and individual components becomes even more critical. Perkins recently highlighted this during the presentation of the new “2600” series, which, with a displacement of 13 liters, will fit into Perkins’ range with a power output between 240 and 515 kilowatts (450 to 690 horsepower), effectively replacing units currently covered by four different series fragmented between 12.5 liters and 18 liters.
This result is made possible by advanced ground-up design of all engine block components, using advanced structural simulations capable of modeling mechanical stresses from peak cylinder pressures of 240 bar, achieved with a common rail system operating at 2,500 bar and compression ratios pushed to 18:1. This leads to specific powers of 55 horsepower per liter, also thanks to a variable geometry turbocharger system.
Structural Simulations and Proprietary Software
Structural simulation is one of the fundamental steps in fine-tuning the unit to achieve the target performance. As Perkins engineers point out, the process begins well before individual engine prototypes are built and continues even after units enter series production. The design starts with the key component of any combustion engine, the crankshaft, sized to ensure robustness and efficiency.
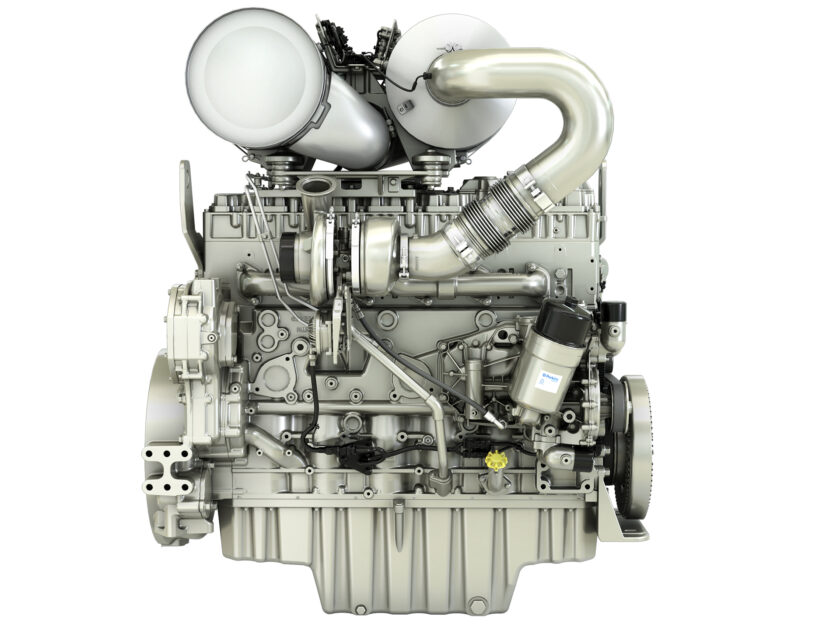
The increase in power densities in recent years has led to the need for smaller crankshafts that must offer greater structural performance in terms of strength and reliability. The same applies to main bearings, which are larger to handle higher loads. Resizing bearings cannot be done randomly, as larger bearings result in greater energy absorption. Thus, each component must be studied to ensure a balance between size, strength, and functionality.
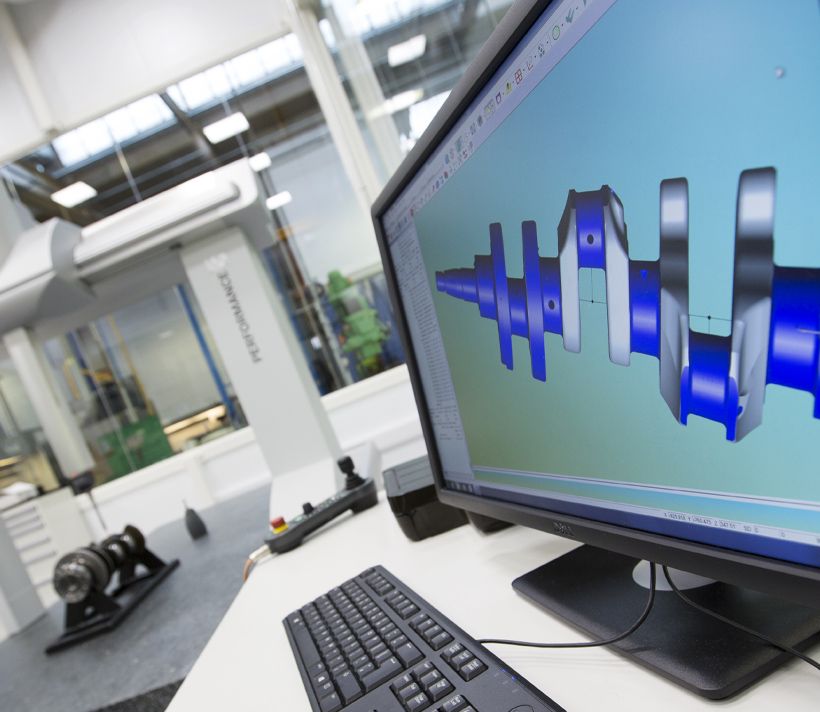
While Perkins today uses the latest generation finite element simulation software available on the market, the design also incorporates proprietary algorithms developed over decades, allowing the engine manufacturer to offer structurally optimized units to maximize specific power without compromising engine reliability.
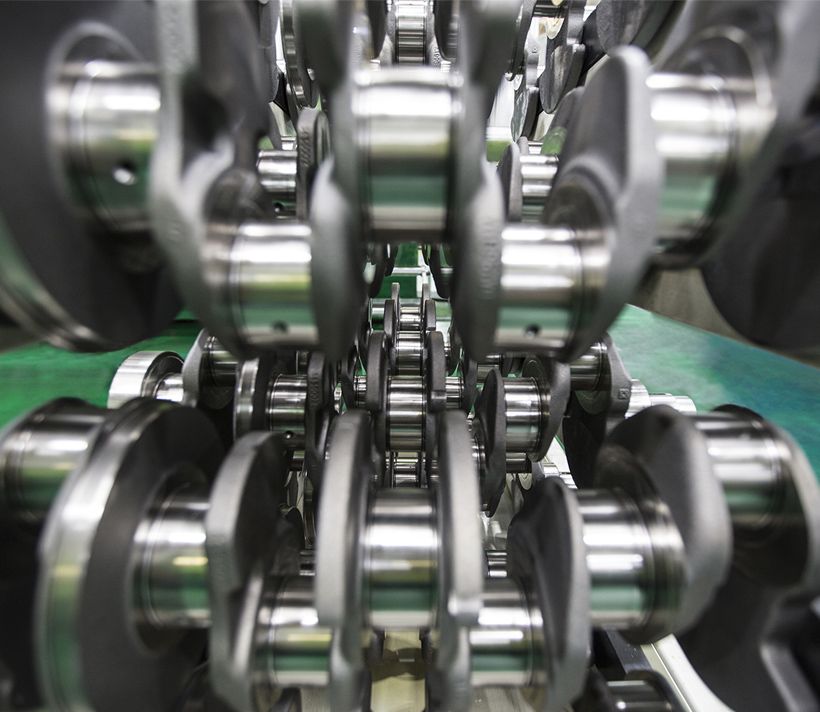
From 10 to 812 Horsepower
Looking at the Stage V compliant range currently offered by Perkins, it is noticeable that the top models of three different series, the “1204,” “1206,” and “2806,” are now offered with twin-turbo setups, pushing specific power above 45 horsepower per liter. With the introduction of the new “2600” series, Perkins will offer a range of power outputs from 10 horsepower for the “400” series twin-cylinder engines to 597 kilowatts (812 horsepower) from the 18-liter six-cylinder engines of the “2800” series.
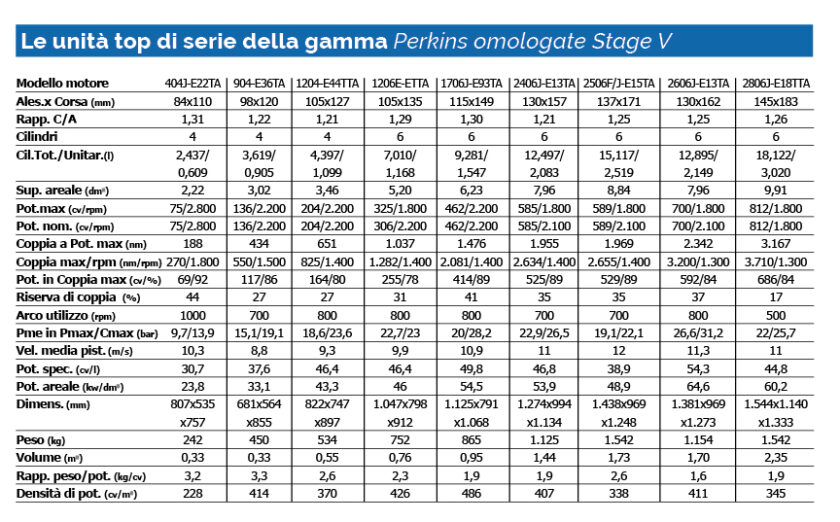
Among these, the most recent units of the “904” and “1200” series stand out. The former features four-cylinder 3.5-liter architectures offering up to 100 kilowatts (136 horsepower) at 2,200 rpm and 550 newton-meters of torque at 1,500 rpm. The latter is divided into four- and six-cylinder engine blocks, with the former offering up to 204 horsepower at 2,200 rpm and the latter reaching 325 horsepower at 1,800 rpm, with torques of 825 and 1,282 newton-meters developed at 1,400 rpm, respectively.
Title: Perkins, Structural Design
Author: Jacopo Oldani
Translation with ChatGPT